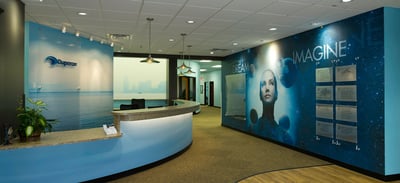
Architects and engineers are smart people who are dedicated to taking the information their clients provide them and designing an aesthetically pleasing and functional building to meet their client’s goals. In their design specifications, they include specific products for building finishes, which they’ve researched or have experienced, to match the desired outcome expressed by their client. Typically, these materials or products have also been discussed with and accepted by the client.
However, during the budgeting and estimating phase of the project, contractors and subcontractors alike may make suggestions for comparable materials/products. This may be because the subcontractor is more experienced with the installation of a certain manufacturer’s product, they know about a considerably less expensive application, or because the specced (specified) product is discontinued or back ordered for an undetermined amount of time. Keeping on schedule is critical for every construction job, so a back ordered item can cause many problems with the flow of a project. Also, what building owner doesn’t have an interest in saving money whenever they can? So, it’s common for a product substitution to be identified and as long as it’s comparable, the architect should sign off to accept it. The architect gets final approval on all substitutions because they have to be back tracked into the original plans and determined whether or not an item needs additional engineering to make the change work seamlessly.
Typically, the building owner is excited to have options because of the cost and time savings, so substitution flexibility is important in the commercial construction industry. This practice can also be considered value engineering, which takes place in other occurrences when an original design comes in over the client’s anticipated budget. Due to time constraints of competitive bidding under the General Construction delivery method, substitutions and value engineering don’t naturally have time to occur. But, the team approach through a Design-Build project is set-up to make exceptions for these recommendations, which is another benefit of how Design-Build is more efficient in saving time and money.